Wi-Fi&BT Dual Mode Module
WB2S Module Datasheet
Product Overview
WB2S is a low-power embedded Wi-Fi+BLE Dual protocol module that Tuya has developed. It consists of a highly integrated RF chip (BK7231T) and several peripheral components, with an embedded Wi-Fi network protocol stack and robust library functions. WB2S also contains a low-power 32-bit microcontroller unit (MCU), 1T1R WLAN module, 256 KB static random-access memory (SRAM), 2 MB flash memory, and extensive peripherals. WB2S is an RTOS platform that integrates all function libraries of the Wi-Fi MAC and TCP/IP protocols. You can develop embedded Wi-Fi products as required.
Features
Embedded low-power 32-bit CPU, which can also function as an application processor
Clock rate: 120 MHz
Working voltage: 3.0 V to 3.6 V
Peripherals: nine GPIOs, one universal asynchronous receiver/transmitter (UART), and one analog-to-digital converter (ADC)
Wi-Fi connectivity
802.11b/g/n
Channels 1 to 14 at 2.4 GHz
WPA and WPA2 security modes
Up to +16 dBm output power in 802.11b mode
EZ net pairing mode for Android and iOS devices
On-board PCB antenna with a gain of -1.0dBi
Working temperature: –20°C to +85°C
BLE Support Bluetooth (V4.0) Maximum output power + 6dBm Onboard PCB antenna
Applications
Intelligent building
Smart household and home appliances
Smart socket and light
Industrial wireless control
Baby monitor
Network camera
ntelligent bus
Change History
No.
Date
Change Description
Version After Change
1
2019-11-22
This is the first release.
1.0.0
Module Interfaces
Dimensions and Footprint
WB2S has two rows of pins with a 2 mm pin spacing. The WB2S dimensions (H x W x D) are 2.8 mm x 15 mm x 18 mm. Note: The default dimensional tolerance is ±0.35 mm. If a customer has other requirements, clearly specify them in the datasheet after communication.
Interface Pin Definition
Pin No.
Symbol
I/O Type
Function
1
VBAT
P
Power supply pin (3.3 V), which is connected to the VBAT pin on the internal IC
2
PWM2
I/O
Common GPIO, which is connected to the P8 pin on the internal IC
3
GND
P
Power supply reference ground pin
4
PWM1
I/O
Common GPIO, which is connected to the P7 pin on the internal IC
5
1RX
I/O
UART1_RXD, which is used as a user-side serial interface pin and is connected to the P10 pin on the internal IC
6
PWM0
I/O
Common GPIO, which is connected to the P6 pin on the internal IC
7
1TX
I/O
UART1_TXD, which is used as a user-side serial interface pin and is connected to the P11 pin on the internal IC
8
AD
AI
ADC pin, which is connected to the P23 pin on the internal IC
9
PWM4
I/O
Common GPIO, which is connected to the P24 pin on the internal IC
10
CEN
I
Low-level reset, high-level active (internally pulled high) Docking IC-CEN
11
PWM5
I/O
Common GPIO, which is connected to the P26 pin on the internal IC
Note: P indicates a power supply pin, I/O indicates an input/output pin, and AI indicates an analog input pin.
Test Pin Definition
Pin No.
Symbol
I/O Type
Function
1
SO
I/O
Data output pin when data is downloaded from the flash memory, which is used for module production and firmware burning andis connected to the P23 or ADC3 pin on the internal IC
2
SI
I/O
Data input pin when data is downloaded from the flash memory, which is used for module production and firmware burning andis connected to the P22 pin on the internal IC
3
CS
I/O
Chip selection pin when data is downloaded from the flash memory, which is used for module production and firmware burning and isconnected to the P21 pin on the internal IC
4
SCK
I/O
Clock pin when data is downloaded from the flash memory, which is used for module production and firmware burning and is connected to the P20 pin on the internal IC
Note: - Test pins are not recommended.
Electrical Parameters
Absolute Electrical Parameters
Parameter
Description
Minimum Value
Maximum Value
Unit
Ts
Storage temperature
–40
150
°C
VCC
Power supply voltage
–0.3
3.6
V
Static electricity voltage (human body model)
Tamb = 25°C
N/A
2
kV
Static electricity voltage (machine model)
Tamb = 25°C
N/A
0.5
kV
Electrical Conditions
Parameter
Description
Minimum Value
Typical Value
Maximum Value
Unit
Ta
Working temperature
–20
N/A
85
°C
VCC
Power supply voltage
3.0
3.3
3.6
V
VIL
I/O low-level input
–0.3
N/A
VCC x 0.25
V
VIH
I/Ohigh-level input
VCC x 0.75
N/A
3.6
V
VOL
I/O low-level output
N/A
N/A
VCC x 0.1
V
VoH
I/O high-level output
VCC x 0.8
N/A
VCC
V
Imax
I/O drive current
N/A
6
15
mA
RF Current Consumption
Working Status
Mode
Rate
TX Power / Receiving
Typical Value
Unit
TX
802.11b
11 Mbit/s
+16 dBm
235
mA
802.11g
54 Mbit/s
+14 dBm
200
mA
802.11n
MCS7
+12 dBm
185
mA
802.11n HT40
MCS7
+12 dBm
190
mA
RX
802.11b
11 Mbit/s
Constant receiving
98
mA
802.11g
54 Mbit/s
Constant receiving
98
mA
802.11n
MCS7
Constant receiving
98
mA
802.11n HT40
MCS7
Constant receiving
116
mA
Working Current
Working Mode
Working Status (Ta = 25°C)
Average Value
Peak Value*(Typical Value)
Unit
Quick connection network status (Bluetooth network)
The module is in the fast network configuration state, and the WIFI indicator flashes quickly
110
310
mA
Fast connection network status (AP network configuration)
The module is in the fast connection network configuration state, the WIFI indicator flashes slowly
80
430
mA
Quick Connect Network Status (EZ Network)
The module is in the fast network configuration state, and the WIFI indicator flashes quickly
80
320
mA
Network connection idle state
The module is connected to the network and the WiFi indicator is always on
50
300
mA
Network connection operation status
The module is connected to the network and the WiFi indicator is always on
50
315
mA
Disconnected status
Module is offline
105
315
mA
RF Features
Basic RF Features
Parameter
Description
Frequency band
2.412 GHz to 2.484 GHz
Wi-Fi standard
IEEE 802.11b/g/n (channels 1 to 14)
BLE standard
BLE 4.0
Data transmission rate
802.11b: 1, 2, 5.5, or 11 (Mbit/s)
802.11g: 6, 9, 12, 18, 24, 36, 48, or 54 (Mbit/s)
802.11n: HT20 MCS0 to MCS7
802.11n: HT40 MCS0 to MCS7
Antenna type
Onboard PCB antenna with a gain of -1 dBi
TX Performance
Parameter
Minimum Value
Typical Value
Maximum Value
Unit
Average RF output power, 802.11b CCK mode 11 Mbit/s
N/A
16
N/A
dBm
Average RF output power, 802.11g OFDM mode 54 Mbit/s
N/A
14
N/A
dBm
Average RF output power, 802.11n OFDM mode MCS7
N/A
13
N/A
dBm
Frequency error
–2
N/A
+2
ppm
EVM under 802.11b CCK, 11 Mbit/s 16 dBm
NA
–18
NA
dB
EVM under 802.11g OFDM, 54 Mbit/s, 14 dBm
–26
–27
–29
dB
EVM under 802.11n OFDM, MCS7, 13 dBm
–26
–27
–28
dB
RX Performance
Parameter
Minimum Value
Typical Value
Maximum Value
Unit
PER < 8%, 802.11b CCK mode 1 Mbit/s
N/A
–85
N/A
dBm
PER < 10%, 802.11g OFDM mode 54 Mbit/s
N/A
–72
N/A
dBm
PER < 10%, 802.11n OFDM mode MCS7
N/A
–68
N/A
dBm
PER < 10%,BLE 1M
NA
–95
NA
dBm
Antenna Information
Antenna Type
WB2S uses an onboard PCB antenna.
Antenna Interference Reduction
To ensure optimal Wi-Fi performance when the Wi-Fi module uses an onboard PCB antenna, it is recommended that the antenna be at least 15 mm away from other metal parts. To prevent adverse impact on the antenna radiation performance, avoid copper or traces along the antenna area on the PCB. Deploy the antenna based on the antenna placement solutions.
Antenna Connector Specifications
WB2S does not use an antenna connector.
Packaging Information and Production Instructions
Mechanical Dimensions
Note: The default dimensional tolerance is ±0.35 mm. If a customer has other requirements, clearly specify them in the datasheet after communication.
Recommended PCB Layout
Note: The default dimensional tolerance is ±0.35 mm. If a customer has other requirements, clearly specify them in the datasheet after communication.
Production Instructions
Use an SMT placement machine to mount the stamp hole module that Tuya produces onto the PCB within 24 hours after the module is unpacked and the firmware is burned. If not, vacuum pack the module again. Bake the module before mounting it onto the PCB. (1) SMT placement equipment i. Reflow soldering machine ii. Automated optical inspection (AOI) equipment iii. Nozzle with a 6 mm to 8 mm diameter (2) Baking equipment i. Cabinet oven ii. Anti-static heat-resistant trays iii. Anti-static heat-resistant gloves
Storage conditions for a delivered module are as follows: (1) The moisture-proof bag is placed in an environment where the temperature is below 30°C and the relative humidity is lower than 85%. (2) The shelf life of a dry-packaged product is 12 months from the date when the product is packaged and sealed. (3) The package contains a humidity indicator card (HIC).
Bake a module based on HIC status as follows when you unpack the module package: (1) If the 30%, 40%, and 50% circles are blue, bake the module for 2 consecutive hours. (2) If the 30% circle is pink, bake the module for 4 consecutive hours. (3) If the 30% and 40% circles are pink, bake the module for 6 consecutive hours. (4) If the 30%, 40%, and 50% circles are pink, bake the module for 12 consecutive hours.
Baking settings: (1) Baking temperature: 125±5°C (2) Alarm temperature: 130°C (3) SMT placement ready temperature after natural cooling: < 36°C (4) Number of drying times: 1 (5) Rebaking condition: The module is not soldered within 12 hours after baking.
Do not use SMT to process modules that have been unpacked for over three months. Electroless nickel immersion gold (ENIG) is used for the PCBs. If the solder pads are exposed to the air for over three months, they will be oxidized severely and dry joints or solder skips may occur. Tuya is not liable for such problems and consequences.
Before SMT placement, take electrostatic discharge (ESD) protective measures.
To reduce the reflow defect rate, draw 10% of the products for visual inspection and AOI before first SMT placement to determine a proper oven temperature and component placement method. Draw 5 to 10 modules every hour from subsequent batches for visual inspection and AOI.
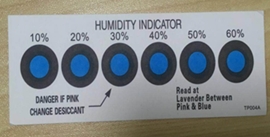
Recommended Oven Temperature Curve
Perform SMT placement based on the following reflow oven temperature curve. The highest temperature is 245°C.
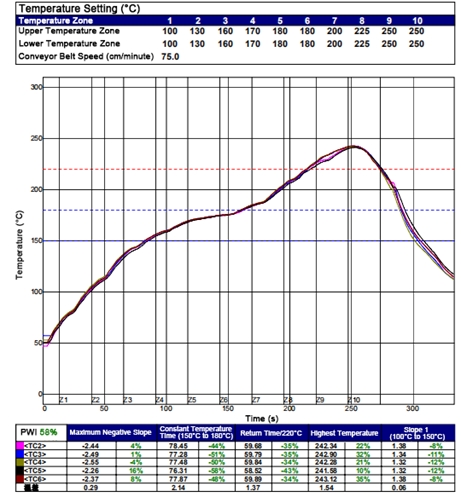
Storage Conditions

MOQ and Packaging Information
Product number
MOQ(pcs)
Shipping packaging method
Modules per reel (pcs)
Packaging reels per box (reels)
WB2S
4000
Tape reel
1000
4
Appendix—Statement
Federal Communications Commission (FCC) Declaration of Conformity FCC Caution: Any changes or modifications not expressly approved by the party responsible for compliance could void the user's authority to operate this equipment. This device complies with Part 15 of the FCC Rules. Operation is subject to the following two conditions: (1) This device may not cause harmful interference, and (2) this device must accept any interference received, including interference that may cause undesired operation. This device and its antenna(s) must not be co-located or operating in conjunction with any other antenna or transmitter. 15.105 Information to the user. (b) For a Class B digital device or peripheral, the instructions furnished the user shall include the following or similar statement, placed in a prominent location in the text of the manual: Note: This equipment has been tested and found to comply with the limits for a Class B digital device, pursuant to part 15 of the FCC Rules. These limits are designed to provide reasonable protection against harmful interference in a residential installation. This equipment generates, uses and can radiate radio frequency energy and, if not installed and used in accordance with the instructions, may cause harmful interference to radio communications. However, there is no guarantee that interference will not occur in a particular installation. If this equipment does cause harmful interference to radio or television reception, which can be determined by turning the equipment off and on, the user is encouraged to try to correct the interference by one or more of the following measures: —Reorient or relocate the receiving antenna. —Increase the separation between the equipment and receiver. —Connect the equipment into an outlet on a circuit different from that to which the receiver is connected. —Consult the dealer or an experienced radio/TV technician for help.
This equipment complies with FCC radiation exposure limits set forth for an uncontrolled environment. This equipment should be installed and operated with minimum distance 20 cm between the radiator and your body.
Radiation Exposure Statement: This equipment complies with FCC radiation exposure limits set forth for an uncontrolled environment. This transmitter must not be co-located or operating in conjunction with any other antenna or transmitter. The availability of some specific channels and/or operational frequency bands is country dependent and firmware programmed at the factory to match the intended destination. The firmware setting is not accessible by the end user.
The final end product must be labeled in a visible area with the following: "Contains Transmitter Module2AFNL-BR3L" This radio module must not be installed to co-locate and operating simultaneously with other radios in host system, additional testing and equipment authorization may be required to operating simultaneously with other radio.
This LMA does not have RF shielding and is tested and approved as standalone configuration, additional evaluation may be required for any system integrated this radio module.
Declaration of Conformity European notice
Hereby, Hangzhou Tuya Information Technology Co., Ltd. declares that this Wi-Fi module product is in compliance with essential requirements and other relevant provisions of Directive 2014/53/EC. A copy of the Declaration of conformity can be found at https://www.tuya.com.
EN 300 328 V2.1.1
EN 301 489-1 V2.1.1; EN 301 489-17 V3.1.1
EN 62311:2008
EN 60950-1:2006+A11:2009+A1:2010+A12:2011+A2:2013
WB1S Module Datasheet
Product Overview
WB1S is a low-power embedded Wi-Fi+BLE Dual protocol module that Tuya has developed. It consists of a highly integrated RF chip (BK7231T) and several peripheral components, with an embedded Wi-Fi network protocol stack and robust library functions. WB1S also contains a low-power 32-bit microcontroller unit (MCU), 1T1R WLAN module, 256 KB static random-access memory (SRAM), 2 MB flash memory, and extensive peripherals. WB1S is an RTOS platform that integrates all function libraries of the Wi-Fi MAC and TCP/IP protocols. You can develop embedded Wi-Fi products as required.
Features
Embedded low-power 32-bit CPU, which can also function as an application processor
Clock rate: 120 MHz
Working voltage: 3.0 V to 3.6 V
Peripherals: nine GPIOs, one universal asynchronous receiver/transmitter (UART), and one analog-to-digital converter (ADC)
Wi-Fi connectivity
802.11b/g/n
Channels 1 to 14 at 2.4 GHz
WPA and WPA2 security modes
Up to +16 dBm output power in 802.11b mode
EZ net pairing mode for Android and iOS devices
On-board PCB antenna
Working temperature: –20°C to +85°C
BLE Support Bluetooth (V4.0) Maximum output power + 6dBm On-board PCB antenna and external antenna IPEX connector
Applications
Intelligent building
Smart household and home appliances
Smart socket and light
Industrial wireless control
Baby monitor
Network camera
ntelligent bus
Change History
No.
Date
Change Description
Version After Change
1
2019-11-22
This is the first release.
1.0.0
Module Interfaces
Dimensions and Footprint
WB1S has two rows of pins with a 2 mm pin spacing. The WB1S dimensions (H x W x D) are 2.8 mm x 16 mm x 23.5 mm. Note: The default dimensional tolerance is ±0.35 mm. If a customer has other requirements, clearly specify them in the datasheet after communication.
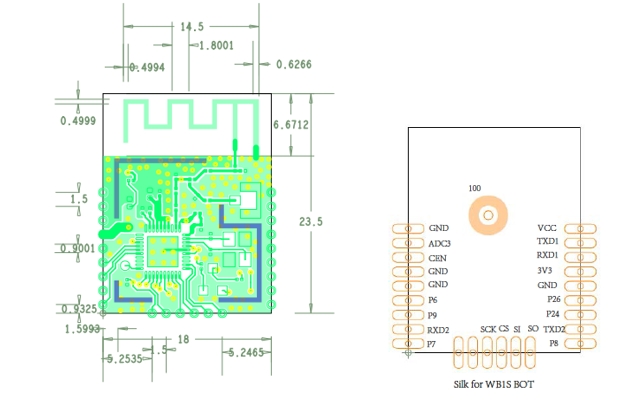
Interface Pin Definition
Pin No.
Symbol
I/O Type
Function
1
VCC
P
Power supply pin (3.3 V)
2
TXD1
I/O
UART1_TXD, which is used as a user-side serial interface pin and connected to the P11 pin on the internal IC
3
RXD1
I/O
UART1_RXD, which is used as a user-side serial interface pin and connected to the P10 pin on the internal IC
4
3V3
P
Power supply pin (3.3 V)
5
GND
P
Power supply reference ground pin
6
P26
I/O
Common I/O pin, which can be used as a hardware PWM pin and is connected to the P26 pin on the internal IC
7
P24
I/O
Common I/O pin, which can be used as a hardware PWM pin and is connected to the P24 pin on the internal IC
8
TXD2
I/O
UART2_TXD, which is used for displaying the module internal information and is connected to the P0 pin on the internal IC
9
P8
I/O
Common I/O pin, which can be used as a hardware PWM pin and is connected to the P8 pin on the internal IC
10
P7
I/O
Common I/O pin, which can be used as a hardware PWM pin and is connected to the P7 pin on the internal IC
11
RXD2
I/O
UART0_RXD, which is used for displaying the module internal information and is connected to the P1 pin on the internal IC
12
P9
I/O
Common I/O pin, which can be used as a hardware PWM pin and is connected to the P9 pin on the internal IC
13
P6
I/O
Common I/O pin, which can be used as a hardware PWM pin and is connected to the P6 pin on the internal IC
14
GND
P
Power supply reference ground pin
15
GND
P
Power supply reference ground pin
16
CEN
I
Low-level reset, high-level active (internally pulled high) Docking IC-CEN
17
ADC3
AI
ADC pin, which is connected to the P23 pin on the internal IC
18
GND
P
Power supply reference ground pin
Note: - P indicates power supply pins, I/O indicates input/output pins, and AI indicates analog input pins. - CEN is only a hardware reset pin and cannot clear the Wi-Fi network configuration.
Test Pin Definition
Pin No.
Symbol
I/O Type
Function
1
SO
I/O
Data output pin when data is downloaded from the flash memory, which is used for module production and firmware burning andis connected to the P23 or ADC3 pin on the internal IC
2
SI
I/O
Data input pin when data is downloaded from the flash memory, which is used for module production and firmware burning andis connected to the P22 pin on the internal IC
3
CS
I/O
Chip selection pin when data is downloaded from the flash memory, which is used for module production and firmware burning and isconnected to the P21 pin on the internal IC
4
SCK
I/O
Clock pin when data is downloaded from the flash memory, which is used for module production and firmware burning and is connected to the P20 pin on the internal IC
Note: - Test pins are not recommended.
Electrical Parameters
Absolute Electrical Parameters
Parameter
Description
Minimum Value
Maximum Value
Unit
Ts
Storage temperature
–40
150
°C
VCC
Power supply voltage
–0.3
3.6
V
Static electricity voltage (human body model)
Tamb = 25°C
N/A
2
kV
Static electricity voltage (machine model)
Tamb = 25°C
N/A
0.5
kV
Electrical Conditions
Parameter
Description
Minimum Value
Typical Value
Maximum Value
Unit
Ta
Working temperature
–20
N/A
85
°C
VCC
Power supply voltage
3.0
3.3
3.6
V
VIL
I/O low-level input
–0.3
N/A
VCC x 0.25
V
VIH
I/Ohigh-level input
VCC x 0.75
N/A
3.6
V
VOL
I/O low-level output
N/A
N/A
VCC x 0.1
V
VoH
I/O high-level output
VCC x 0.8
N/A
VCC
V
Imax
I/O drive current
N/A
6
15
mA
RF Current Consumption
Working Status
Mode
Rate
TX Power / Receiving
Typical Value
Unit
TX
802.11b
11 Mbit/s
+16 dBm
222
mA
802.11g
54 Mbit/s
+14 dBm
195
mA
802.11n
MCS7
+12 dBm
185
mA
802.11n HT40
MCS7
+12 dBm
190
mA
RX
802.11b
11 Mbit/s
Constant receiving
98
mA
802.11g
54 Mbit/s
Constant receiving
98
mA
802.11n
MCS7
Constant receiving
98
mA
802.11n HT40
MCS7
Constant receiving
116
mA
Working Current
Working Mode
Working Status (Ta = 25°C)
Average Value
Peak Value*(Typical Value)
Unit
Quick connection network status (Bluetooth network)
The module is in the fast network configuration state, and the WIFI indicator flashes quickly
100
260
mA
Fast connection network status (AP network configuration)
The module is in the fast connection network configuration state, the WIFI indicator flashes slowly
80
360
mA
Quick Connect Network Status (EZ Network)
The module is in the fast network configuration state, and the WIFI indicator flashes quickly
80
320
mA
Network connection idle state
The module is connected to the network and the WiFi indicator is always on
50
250
mA
Network connection operation status
The module is connected to the network and the WiFi indicator is always on
60
260
mA
Disconnected status
Module is offline
105
250
mA
RF Features
Basic RF Features
Parameter
Description
Frequency band
2.412 GHz to 2.484 GHz
Wi-Fi standard
IEEE 802.11b/g/n (channels 1 to 14)
BLE standard
BLE 4.0
Data transmission rate
802.11b: 1, 2, 5.5, or 11 (Mbit/s)
802.11g: 6, 9, 12, 18, 24, 36, 48, or 54 (Mbit/s)
802.11n: HT20 MCS0 to MCS7
802.11n: HT40 MCS0 to MCS7
Antenna type
Onboard PCB antenna with a gain of 0.5 dBi
TX Performance
Parameter
Minimum Value
Typical Value
Maximum Value
Unit
Average RF output power, 802.11b CCK mode 11 Mbit/s
N/A
16
N/A
dBm
Average RF output power, 802.11g OFDM mode 54 Mbit/s
N/A
14
N/A
dBm
Average RF output power, 802.11n OFDM mode MCS7
N/A
13
N/A
dBm
Frequency error
–2
N/A
+2
ppm
EVM under 802.11b CCK, 11 Mbit/s 16 dBm
–18
dB
EVM under 802.11g OFDM, 54 Mbit/s, 14 dBm
–30
–29
–25
dB
EVM under 802.11n OFDM, MCS7, 13 dBm
–31
–28
–27
dB
RX Performance
Parameter
Minimum Value
Typical Value
Maximum Value
Unit
PER < 8%, 802.11b CCK mode 1 Mbit/s
N/A
–92
N/A
dBm
PER < 10%, 802.11g OFDM mode 54 Mbit/s
N/A
–75
N/A
dBm
PER < 10%, 802.11n OFDM mode MCS7
N/A
–68
N/A
dBm
PER < 10%,BLE 1M
NA
–95
NA
dBm
Antenna Information
Antenna Type
The default method is a PCB onboard antenna
Antenna Interference Reduction
To ensure optimal Wi-Fi performance when the Wi-Fi module uses an onboard PCB antenna, it is recommended that the antenna be at least 15 mm away from other metal parts. To prevent adverse impact on the antenna radiation performance, avoid copper or traces along the antenna area on the PCB. Deploy the antenna based on the antenna placement solutions, as shown in the following figure
Antenna Connector Specifications
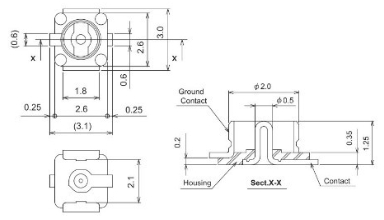
Packaging Information and Production Instructions
Mechanical Dimensions
Note: The default dimensional tolerance is ±0.35 mm. If a customer has other requirements, clearly specify them in the datasheet after communication.
Recommended PCB Layout
Note: The default dimensional tolerance is ±0.35 mm. If a customer has other requirements, clearly specify them in the datasheet after communication.
Production Instructions
Use an SMT placement machine to mount the stamp hole module that Tuya produces onto the PCB within 24 hours after the module is unpacked and the firmware is burned. If not, vacuum pack the module again. Bake the module before mounting it onto the PCB. (1) SMT placement equipment i. Reflow soldering machine ii. Automated optical inspection (AOI) equipment iii. Nozzle with a 6 mm to 8 mm diameter (2) Baking equipment i. Cabinet oven ii. Anti-static heat-resistant trays iii. Anti-static heat-resistant gloves
Storage conditions for a delivered module are as follows: (1) The moisture-proof bag is placed in an environment where the temperature is below 30°C and the relative humidity is lower than 85%. (2) The shelf life of a dry-packaged product is 12 months from the date when the product is packaged and sealed. (3) The package contains a humidity indicator card (HIC).
Bake a module based on HIC status as follows when you unpack the module package: (1) If the 30%, 40%, and 50% circles are blue, bake the module for 2 consecutive hours. (2) If the 30% circle is pink, bake the module for 4 consecutive hours. (3) If the 30% and 40% circles are pink, bake the module for 6 consecutive hours. (4) If the 30%, 40%, and 50% circles are pink, bake the module for 12 consecutive hours.
Baking settings: (1) Baking temperature: 125±5°C (2) Alarm temperature: 130°C (3) SMT placement ready temperature after natural cooling: < 36°C (4) Number of drying times: 1 (5) Rebaking condition: The module is not soldered within 12 hours after baking.
Do not use SMT to process modules that have been unpacked for over three months. Electroless nickel immersion gold (ENIG) is used for the PCBs. If the solder pads are exposed to the air for over three months, they will be oxidized severely and dry joints or solder skips may occur. Tuya is not liable for such problems and consequences.
Before SMT placement, take electrostatic discharge (ESD) protective measures.
To reduce the reflow defect rate, draw 10% of the products for visual inspection and AOI before first SMT placement to determine a proper oven temperature and component placement method. Draw 5 to 10 modules every hour from subsequent batches for visual inspection and AOI.
Recommended Oven Temperature Curve
Perform SMT placement based on the following reflow oven temperature curve. The highest temperature is 245°C.
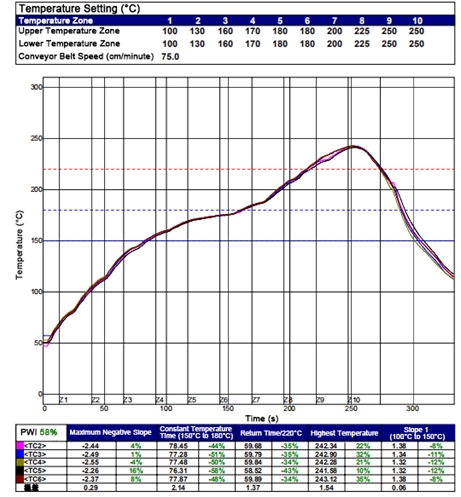
Storage Conditions

MOQ and Packaging Information
Product number
MOQ(pcs)
Shipping packaging method
Modules per reel (pcs)
Packaging reels per box (reels)
WB1S
4000
Tape reel
1000
4
Appendix—Statement
Federal Communications Commission (FCC) Declaration of Conformity FCC Caution: Any changes or modifications not expressly approved by the party responsible for compliance could void the user's authority to operate this equipment. This device complies with Part 15 of the FCC Rules. Operation is subject to the following two conditions: (1) This device may not cause harmful interference, and (2) this device must accept any interference received, including interference that may cause undesired operation. This device and its antenna(s) must not be co-located or operating in conjunction with any other antenna or transmitter. 15.105 Information to the user. (b) For a Class B digital device or peripheral, the instructions furnished the user shall include the following or similar statement, placed in a prominent location in the text of the manual: Note: This equipment has been tested and found to comply with the limits for a Class B digital device, pursuant to part 15 of the FCC Rules. These limits are designed to provide reasonable protection against harmful interference in a residential installation. This equipment generates, uses and can radiate radio frequency energy and, if not installed and used in accordance with the instructions, may cause harmful interference to radio communications. However, there is no guarantee that interference will not occur in a particular installation. If this equipment does cause harmful interference to radio or television reception, which can be determined by turning the equipment off and on, the user is encouraged to try to correct the interference by one or more of the following measures: —Reorient or relocate the receiving antenna. —Increase the separation between the equipment and receiver. —Connect the equipment into an outlet on a circuit different from that to which the receiver is connected. —Consult the dealer or an experienced radio/TV technician for help.
This equipment complies with FCC radiation exposure limits set forth for an uncontrolled environment. This equipment should be installed and operated with minimum distance 20 cm between the radiator and your body.
Radiation Exposure Statement: This equipment complies with FCC radiation exposure limits set forth for an uncontrolled environment. This transmitter must not be co-located or operating in conjunction with any other antenna or transmitter. The availability of some specific channels and/or operational frequency bands is country dependent and firmware programmed at the factory to match the intended destination. The firmware setting is not accessible by the end user.
The final end product must be labeled in a visible area with the following: "Contains Transmitter Module2AFNL-BR3L" This radio module must not be installed to co-locate and operating simultaneously with other radios in host system, additional testing and equipment authorization may be required to operating simultaneously with other radio.
This LMA does not have RF shielding and is tested and approved as standalone configuration, additional evaluation may be required for any system integrated this radio module.
Declaration of Conformity European notice
Hereby, Hangzhou Tuya Information Technology Co., Ltd. declares that this Wi-Fi module product is in compliance with essential requirements and other relevant provisions of Directive 2014/53/EC. A copy of the Declaration of conformity can be found at https://www.tuya.com.
EN 300 328 V2.1.1
EN 301 489-1 V2.1.1; EN 301 489-17 V3.1.1
EN 62311:2008
EN 60950-1:2006+A11:2009+A1:2010+A12:2011+A2:2013
WB3S Module Datasheet
Product Overview
WB3S is a low-power embedded Wi-Fi+BLE Dual protocol module that Tuya has developed. It consists of a highly integrated RF chip (BK7231T) and several peripheral components, with an embedded Wi-Fi network protocol stack and robust library functions. WB3S also contains a low-power 32-bit microcontroller unit (MCU), 1T1R WLAN module, 256 KB static random-access memory (SRAM), 2 MB flash memory, and extensive peripherals. WB3S is an RTOS platform that integrates all function libraries of the Wi-Fi MAC and TCP/IP protocols. You can develop embedded Wi-Fi products as required.
Features
Embedded low-power 32-bit CPU, which can also function as an application processor
Clock rate: 120 MHz
Working voltage: 3.0 V to 3.6 V
Peripherals: nine GPIOs, one universal asynchronous receiver/transmitter (UART), and one analog-to-digital converter (ADC)
Wi-Fi connectivity
802.11b/g/n
Channels 1 to 14 at 2.4 GHz
WPA and WPA2 security modes
Up to +16 dBm output power in 802.11b mode
EZ net pairing mode for Android and iOS devices O- nboard PCB antenna with a gain of 2.3 dBi
Working temperature: –20°C to +85°C
BLE Support Bluetooth (V4.0) Maximum output power + 6dBm Onboard PCB antenna with a gain of 1.5 dBi
Applications
Intelligent building
Smart household and home appliances
Smart socket and light
Industrial wireless control
Baby monitor
Network camera
ntelligent bus
Change History
No.
Date
Change Description
Version After Change
1
2019-11-22
This is the first release.
1.0.0
Module Interfaces
Dimensions and Footprint
WB3S has two rows of pins with a 2 mm pin spacing. The WB3S dimensions (H x W x D) are 2.8 mm x 16 mm x 24 mm. Note: The default dimensional tolerance is ±0.35 mm. If a customer has other requirements, clearly specify them in the datasheet after communication.
Interface Pin Definition
Pin No.
Symbol
I/O Type
Function
1
CEN
I
Low-level reset, high-level active (internally pulled high) Docking IC-CEN
2
ADC3
AI
ADC pin, which is connected to the P23 pin on the internal IC
3
EN
Input
Enabling pin, which is internally pulled up and compatible with other module design
4
P14
I/O
Common GPIO, which is connected to the P14 pin on the internal IC
5
PWM5
I/O
GPIOP_26, which is connected to the P26 pin on the internal IC
6
PWM4
I/O
GPIOP_24, common GPIO, which is connected to the P24 pin on the internal IC
7
PWM0
I/O
GPIOP_6, which is connected to the P6 pin on the internal IC
8
VCC
P
Power supply pin (3.3 V)
9
GND
P
Power supply reference ground pin
10
PWM1
I/O
GPIOP_7, which is connected to the P7 pin on the internal IC
11
TXD2
I/O
UART2_TXD, which is used for displaying the module internal information and is connected to the P0 pin on the internal IC
12
RXD2
I/O
UART0_RXD, which is used to display the module internal information and connected to the P1 pin on the internal IC
13
PWM3
I/O
GPIOP_9, common GPIO, which is connected to the P9 pin on the internal IC
14
PWM2
I/O
GPIOP_8, which is connected to the P8 pin on the internal IC
15
RXD1
I/O
UART1_RXD, which is used as a user-side serial interface pin and is connected to the P10 pin on the internal IC
16
TXD1
I/O
UART1_TXD, which is used as a user-side serial interface pin and is connected to the P11 pin on the internal IC
Note: - P indicates power supply pins, I/O indicates input/output pins, and AI indicates analog input pins. - CEN is only a hardware reset pin and cannot clear the Wi-Fi network configuration. - UART1 is a user-side serial interface pin, which generates information when the module is powered on and starts.
Test Pin Definition
Pin No.
Symbol
I/O Type
Function
1
SO
I/O
Data output pin when data is downloaded from the flash memory, which is used for module production and firmware burning andis connected to the P23 or ADC3 pin on the internal IC
2
SI
I/O
Data input pin when data is downloaded from the flash memory, which is used for module production and firmware burning andis connected to the P22 pin on the internal IC
3
CS
I/O
Chip selection pin when data is downloaded from the flash memory, which is used for module production and firmware burning and isconnected to the P21 pin on the internal IC
4
SCK
I/O
Clock pin when data is downloaded from the flash memory, which is used for module production and firmware burning and is connected to the P20 pin on the internal IC
Note: - Test pins are not recommended.
Electrical Parameters
Absolute Electrical Parameters
Parameter
Description
Minimum Value
Maximum Value
Unit
Ts
Storage temperature
–40
150
°C
VCC
Power supply voltage
–0.3
3.6
V
Static electricity voltage (human body model)
Tamb = 25°C
N/A
2
kV
Static electricity voltage (machine model)
Tamb = 25°C
N/A
0.5
kV
Electrical Conditions
Parameter
Description
Minimum Value
Typical Value
Maximum Value
Unit
Ta
Working temperature
–20
N/A
85
°C
VCC
Power supply voltage
3.0
3.3
3.6
V
VIL
I/O low-level input
–0.3
N/A
VCC x 0.25
V
VIH
I/Ohigh-level input
VCC x 0.75
N/A
3.6
V
VOL
I/O low-level output
N/A
N/A
VCC x 0.1
V
VoH
I/O high-level output
VCC x 0.8
N/A
VCC
V
Imax
I/O drive current
N/A
6
15
mA
RF Current Consumption
Working Status
Mode
Rate
TX Power / Receiving
Typical Value
Unit
TX
802.11b
11 Mbit/s
+16 dBm
222
mA
802.11g
54 Mbit/s
+14 dBm
195
mA
802.11n HT20
MCS7
+12 dBm
185
mA
802.11n HT40
MCS7
+12 dBm
190
mA
RX
802.11b
11 Mbit/s
Constant receiving
98
mA
802.11g
54 Mbit/s
Constant receiving
98
mA
802.11n HT20
MCS7
Constant receiving
98
mA
802.11n HT40
MCS7
Constant receiving
116
mA
Working Current
Working Mode
Working Status (Ta = 25°C)
Average Value
Peak Value*(Typical Value)
Unit
Quick connection network status (Bluetooth network)
The module is in the fast network configuration state, and the WIFI indicator flashes quickly
100
260
mA
Fast connection network status (AP network configuration)
The module is in the fast connection network configuration state, the WIFI indicator flashes slowly
70
305
mA
Quick Connect Network Status (EZ Network)
The module is in the fast network configuration state, and the WIFI indicator flashes quickly
60
300
mA
Network connection idle state
The module is connected to the network and the WiFi indicator is always on
40
270
mA
Network connection operation status
The module is connected to the network and the WiFi indicator is always on
50
280
mA
Disconnected status
Module is offline
100
260
mA
RF Features
Basic RF Features
Parameter
Description
Frequency band
2.412 GHz to 2.484 GHz
Wi-Fi standard
IEEE 802.11b/g/n (channels 1 to 14)
BLE standard
BLE 4.0
Data transmission rate
802.11b: 1, 2, 5.5, or 11 (Mbit/s)
802.11g: 6, 9, 12, 18, 24, 36, 48, or 54 (Mbit/s)
802.11n: HT20 MCS0 to MCS7
802.11n: HT40 MCS0 to MCS7
Antenna type
Onboard PCB antenna with a gain of 2.3 dBi
TX Performance
Parameter
Minimum Value
Typical Value
Maximum Value
Unit
Average RF output power, 802.11b CCK mode 11 Mbit/s
N/A
16
N/A
dBm
Average RF output power, 802.11g OFDM mode 54 Mbit/s
N/A
14
N/A
dBm
Average RF output power, 802.11n OFDM mode MCS7
N/A
13
N/A
dBm
Frequency error
–2
N/A
+2
ppm
EVM under 802.11b CCK, 11 Mbit/s 16 dBm
–18
dB
EVM under 802.11g OFDM, 54 Mbit/s, 14 dBm
–26
–27
–29
dB
EVM under 802.11n OFDM, MCS7, 13 dBm
–26
–27
–29
dB
RX Performance
Parameter
Minimum Value
Typical Value
Maximum Value
Unit
PER < 8%, 802.11b CCK mode 1 Mbit/s
N/A
–92
N/A
dBm
PER < 10%, 802.11g OFDM mode 54 Mbit/s
N/A
–75
N/A
dBm
PER < 10%, 802.11n OFDM mode MCS7
N/A
–68
N/A
dBm
PER < 10%,BLE 1M
NA
–95
NA
dBm
Antenna Information
Antenna Type
WB3S uses an onboard PCB antenna.
Antenna Interference Reduction
To ensure optimal Wi-Fi performance when the Wi-Fi module uses an onboard PCB antenna, it is recommended that the antenna be at least 15 mm away from other metal parts. To prevent adverse impact on the antenna radiation performance, avoid copper or traces along the antenna area on the PCB. Deploy the antenna based on the antenna placement solutions, as shown in the following figure
Antenna Connector Specifications
WB3S does not use an antenna connector.
Packaging Information and Production Instructions
Mechanical Dimensions
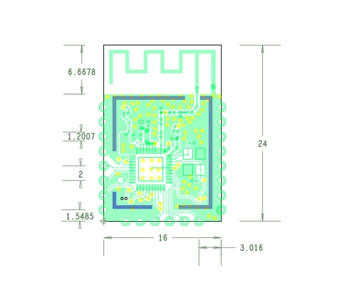
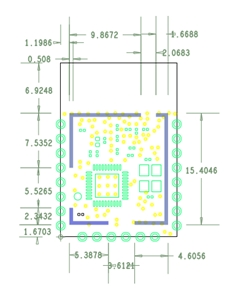
Note: The default dimensional tolerance is ±0.35 mm. If a customer has other requirements, clearly specify them in the datasheet after communication.
Recommended PCB Layout
Note: The default dimensional tolerance is ±0.35 mm. If a customer has other requirements, clearly specify them in the datasheet after communication.
Production Instructions
Use an SMT placement machine to mount the stamp hole module that Tuya produces onto the PCB within 24 hours after the module is unpacked and the firmware is burned. If not, vacuum pack the module again. Bake the module before mounting it onto the PCB. (1) SMT placement equipment i. Reflow soldering machine ii. Automated optical inspection (AOI) equipment iii. Nozzle with a 6 mm to 8 mm diameter (2) Baking equipment i. Cabinet oven ii. Anti-static heat-resistant trays iii. Anti-static heat-resistant gloves
Storage conditions for a delivered module are as follows: (1) The moisture-proof bag is placed in an environment where the temperature is below 30°C and the relative humidity is lower than 85%. (2) The shelf life of a dry-packaged product is 12 months from the date when the product is packaged and sealed. (3) The package contains a humidity indicator card (HIC).
Bake a module based on HIC status as follows when you unpack the module package: (1) If the 30%, 40%, and 50% circles are blue, bake the module for 2 consecutive hours. (2) If the 30% circle is pink, bake the module for 4 consecutive hours. (3) If the 30% and 40% circles are pink, bake the module for 6 consecutive hours. (4) If the 30%, 40%, and 50% circles are pink, bake the module for 12 consecutive hours.
Baking settings: (1) Baking temperature: 125±5°C (2) Alarm temperature: 130°C (3) SMT placement ready temperature after natural cooling: < 36°C (4) Number of drying times: 1 (5) Rebaking condition: The module is not soldered within 12 hours after baking.
Do not use SMT to process modules that have been unpacked for over three months. Electroless nickel immersion gold (ENIG) is used for the PCBs. If the solder pads are exposed to the air for over three months, they will be oxidized severely and dry joints or solder skips may occur. Tuya is not liable for such problems and consequences.
Before SMT placement, take electrostatic discharge (ESD) protective measures.
To reduce the reflow defect rate, draw 10% of the products for visual inspection and AOI before first SMT placement to determine a proper oven temperature and component placement method. Draw 5 to 10 modules every hour from subsequent batches for visual inspection and AOI.
Recommended Oven Temperature Curve
Perform SMT placement based on the following reflow oven temperature curve. The highest temperature is 245°C.
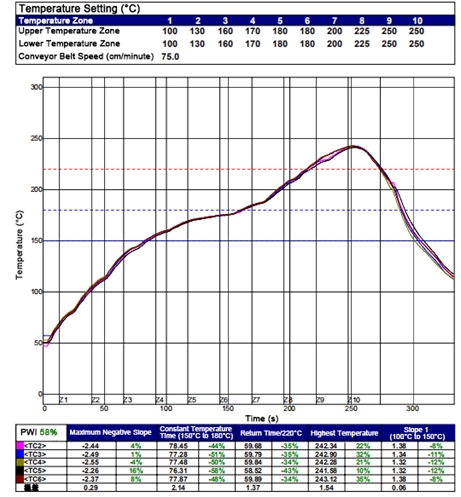
Storage Conditions

MOQ and Packaging Information
Product number
MOQ(pcs)
Shipping packaging method
Modules per reel (pcs)
Packaging reels per box (reels)
WB3S
4000
Tape reel
1000
4
Appendix—Statement
Federal Communications Commission (FCC) Declaration of Conformity FCC Caution: Any changes or modifications not expressly approved by the party responsible for compliance could void the user's authority to operate this equipment. This device complies with Part 15 of the FCC Rules. Operation is subject to the following two conditions: (1) This device may not cause harmful interference, and (2) this device must accept any interference received, including interference that may cause undesired operation. This device and its antenna(s) must not be co-located or operating in conjunction with any other antenna or transmitter. 15.105 Information to the user. (b) For a Class B digital device or peripheral, the instructions furnished the user shall include the following or similar statement, placed in a prominent location in the text of the manual: Note: This equipment has been tested and found to comply with the limits for a Class B digital device, pursuant to part 15 of the FCC Rules. These limits are designed to provide reasonable protection against harmful interference in a residential installation. This equipment generates, uses and can radiate radio frequency energy and, if not installed and used in accordance with the instructions, may cause harmful interference to radio communications. However, there is no guarantee that interference will not occur in a particular installation. If this equipment does cause harmful interference to radio or television reception, which can be determined by turning the equipment off and on, the user is encouraged to try to correct the interference by one or more of the following measures: —Reorient or relocate the receiving antenna. —Increase the separation between the equipment and receiver. —Connect the equipment into an outlet on a circuit different from that to which the receiver is connected. —Consult the dealer or an experienced radio/TV technician for help.
This equipment complies with FCC radiation exposure limits set forth for an uncontrolled environment. This equipment should be installed and operated with minimum distance 20 cm between the radiator and your body.
Radiation Exposure Statement: This equipment complies with FCC radiation exposure limits set forth for an uncontrolled environment. This transmitter must not be co-located or operating in conjunction with any other antenna or transmitter. The availability of some specific channels and/or operational frequency bands is country dependent and firmware programmed at the factory to match the intended destination. The firmware setting is not accessible by the end user.
The final end product must be labeled in a visible area with the following: "Contains Transmitter Module2AFNL-BR3L" This radio module must not be installed to co-locate and operating simultaneously with other radios in host system, additional testing and equipment authorization may be required to operating simultaneously with other radio.
This LMA does not have RF shielding and is tested and approved as standalone configuration, additional evaluation may be required for any system integrated this radio module.
Declaration of Conformity European notice
Hereby, Hangzhou Tuya Information Technology Co., Ltd. declares that this Wi-Fi module product is in compliance with essential requirements and other relevant provisions of Directive 2014/53/EC. A copy of the Declaration of conformity can be found at https://www.tuya.com.
EN 300 328 V2.1.1
EN 301 489-1 V2.1.1; EN 301 489-17 V3.1.1
EN 62311:2008
EN 60950-1:2006+A11:2009+A1:2010+A12:2011+A2:2013
WB3L Module Datasheet
Product Overview
WB3L is a low-power embedded Wi-Fi and BLE module that Tuya has developed. It consists of a highly integrated RF chip (BK7231T) and several peripheral components, with an embedded Wi-Fi network protocol stack and robust library functions. WB3L is embedded with a low-power 32-bit microcontroller unit (MCU), 2 MB flash memory, 256 KB static random-access memory (SRAM), and extensive peripherals. WB3L is an RTOS platform that integrates all function libraries of the Wi-Fi MAC andTCP/IP protocols. You can develop embedded Wi-Fi products as required.
Features
Embedded low-power 32-bit CPU, which can also function as an application processor
Dominant frequency: 120 MHz
Working voltage: 3.0 V to 3.6 V
Peripherals: 8 GPIOs
Wi-Fi connectivity
802.11 b/g/n
Channels 1 to 14 at 2.4 GHz
WPA and WPA2 security modes
Up to +17 dBm output power in 802.11b mode
STA, AP, and STA+AP working modes
EZ and AP net pairing modes for Android and iOS devices
Onboard PCB antenna with a gain of 1.2 dBi
Working temperature: –40°C to +105°C
BLE connectivity
Support for Bluetooth 4.0
Maximum output power of +6 dBm
Onboard PCB antenna with a gain of 1.2 dBi
Applications
Intelligent building
Smart household and home appliances
Smart socket and light
Industrial wireless control
Baby monitor
Network camera
Intelligent bus
Change History
No.
Date
Change Description
Version After Change
1
2019-11-17
This is the first release.
V1.0.0
Module Interfaces
Dimensions and Footprint
WB3L has two rows of pins with a 2±0.1 mm pin spacing.
The WB3L dimensions (H x W x D) are 2.8±0.15 mm x 16±0.35 mm x 24±0.35 mm. Figure shows the WB3L front and rear views.
Interface Pin Definition
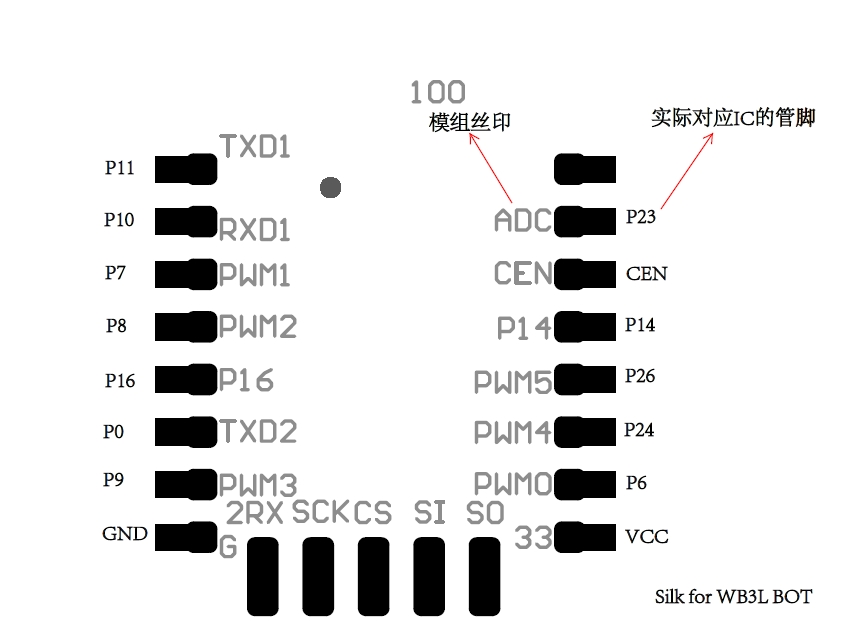
Pin No.
Symbol
I/O Type
Function
1
RST
I/O
Reset pin, which is disconnected
2
ADC
AI
ADC pin, which is connected to the P23 pin on the internal IC
3
EN
I
Module enabling pin, which is connected to 3.3 V for normal use
4
P14
I/O
Common I/O pin, which is connected to the P14 pin on the internal IC
5
PWM5
I/O
Hardware PWM pin, which is connected to the P26 pin on the internal IC
6
PWM4
I/O
Hardware PWM pin, which is connected to the P24 pin on the internal IC
7
PWM0
I/O
Hardware PWM pin, which is connected to the P6 pin on the internal IC
8
VCC
P
Power supply pin (3.3 V)
9
GND
P
Ground pin
10
PWM3
I/O
Hardware PWM pin, which is connected to the P9 pin on the internal IC
11
TXD2
I/O
UART2_TX, which is connected to the P0 pin on the internal IC
12
P16
I/O
Common I/O pin, which is connected to the P16 pin on the internal IC
13
PWM2
I/O
Hardware PWM pin, which is connected to the P8 pin on the internal IC
14
PWM1
I/O
Hardware PWM pin, which is connected to the P7 pin on the internal IC
15
RXD1
I/O
Serial interface receiving pin (UART_RX), which is connected to the P10 pin on the internal IC
16
TXD1
I/O
Serial interface transmission pin (UART_TX), which is connected to the P11 pin on the internal IC
Note:P indicates a power supply pin, I/O indicates an input/output pin, and AI indicates an analog input pin.
Test Pin Definition
Pin No.
Symbol
I/O Type
Function
TP6
U2_RXD
I/O
UART2_RX, which is connected to the P1 pin on the internal IC
TP2
F_SCK
I/O
Clock pin when data is downloaded from the flash memory, which is connected to the P20 pin on the internal IC
TP3
F_CSN
I/O
Command enabling pin when data is downloaded from the flash memory, which is connected to the P21 pin on the internal IC
TP5
F_SO
I/O
Data input pin when data is downloaded from the flash memory, which is connected to the P22 pin on the internal IC
Electrical Parameters
Absolute Electrical Parameters
Parameter
Description
Minimum Value
Maximum Value
Unit
Ts
Storage temperature
-40
105
℃
VBAT
Power supply voltage
3.0
3.6
V
Static electricity voltage (human body model)
TAMB-25℃
-
2
KV
Static electricity voltage (machine model)
TAMB-25℃
-
0.5
KV
Working Conditions
Parameter
Description
Minimum Value
Typical Value
Maximum Value
Unit
Ta
Working temperature
-40
-
105
℃
VBAT
Power supply voltage
3.0
3.3
3.6
V
VIL
I/O low-level input
-0.3
-
VCC*0.25
V
VIH
I/O high-level input
VCC*0.75
-
VCC
V
VOL
I/O low-level output
-
-
VCC*0.1
V
VoH
I/O high-level output
VCC*0.8
-
VCC
V
Imax
I/O drive current
-
-
12
mA
Current consumption during constant transmission and receiving
Working Status
Mode
Rate
TX Power/ Receiving
Typical Value
Maximum Value
Unit
TX
11b
11Mbps
+17dBm
295
354
mA
TX
11g
54Mbps
+13.5dBm
266
300
mA
TX
11n
MCS7
+13dBm
260
290
mA
RX
11b
11Mbps
Constant receiving
98
100
mA
RX
11g
54Mbps
Constant receiving
98
100
mA
RX
11n
MCS7
Constant receiving
98
100
mA
Working Current
Working Mode
Working Status (Ta = 25°C)
Average Value
Maximum Value
Unit
EZ
The module is in EZ mode, and the Wi-Fi indicator blinks quickly.
95
402
mA
AP
The module is in AP mode, and the Wi-Fi indicator blinks slowly.
106
386
mA
Connected
The module is connected to the network, and the Wi-Fi indicator is steady on.
55
132
mA
Disconnected
The module is disconnected from the network, and the Wi-Fi indicator is steady off.
38
206
mA
RF Features
Basic RF Features
Parameter
Description
Frequency band
2.412~2.484GHz
Wi-Fi standard
IEEE 802.11b/g/n(channels1-14)
Data transmission rate
11b:1,2,5.5, 11 (Mbps); 11g:6,9,12,18,24,36,48,54(Mbps); 11n: HT20 MCS07; HT40 MCS07
Antenna type
PCB antenna with a gain of 1.2 dBi
TX Performance
Performance during constant transmission
Parameter
Minimum Value
Typical Value
Maximum Value
Unit
Average RF output power,802.11b CCK Mode 11M
-
16
-
dBm
Average RF output power,802.11g OFDM Mode 54M
-
14
-
dBm
Average RF output power,802.11n OFDM Mode MCS7
-
12
-
dBm
Frequency error
-10
-
10
ppm
RX Performance
RX sensitivity
Parameter
Minimum Value
Typical Value
Maximum Value
Unit
PER<8%,RX sensitivity,802.11b DSSS Mode 11M
-
-85
-
dBm
PER<10%,RX sensitivity,802.11g OFDM Mode 54M
-
-72
-
dBm
PER<10%,RX sensitivity,802.11n OFDM Mode MCS7
-
-68
-
dBm
Antenna Information
Antenna Type
WB3L uses an onboard PCB antenna.
Antenna Interference Reduction
To ensure optimal Wi-Fi performance when the Wi-Fi module uses an onboard PCB antenna, it is recommended that the antenna be at least 15mm away from other metal parts. To prevent adverse impact on the antenna radiation performance, avoid copper or traces along the antenna area on the PCB. The following describes three antenna placement solutions: 1.Place the antenna outside the PCB frame. 2.Place the antenna along the PCB frame without copper nearby. 3. Place the antenna in a carved area on the PCB. The preceding solutions ensure that there are no substrate media above or below the antenna and that copper is at a certain distance away from the antenna to maximize the antenna radiation performance.
Packaging Information and Production Instructions
Mechanical Dimensions
The PCB dimensions (W x L x H) are 16±0.35mm (W)×24±0.35mm (L) ×2.8±0.15mm (H)。
Side view

Recommended Schematic Encapsulation
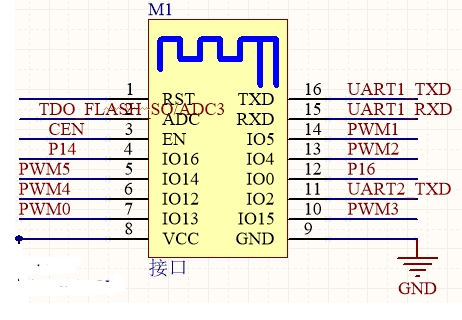
Recommended PCB Encapsulation-Pin header
WB3L can be mounted onto a PCB by using an SMT placement machine or through-hole mounted onto the PCB through a pin header.
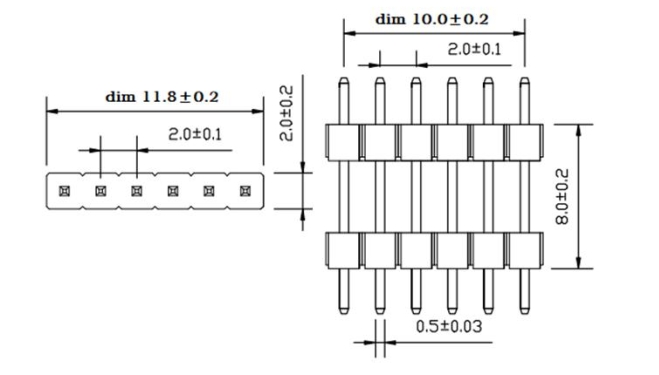
Recommended PCB Encapsulation-SMT
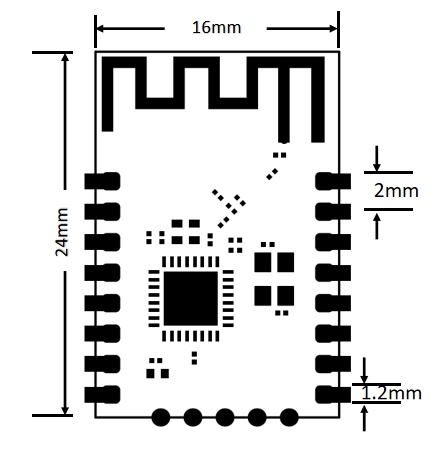
Production Instructions
Use an SMT placement machine to mount components to the stamp hole module that Tuya produces within 24 hours after the module is unpacked and the firmware is burned. If not, vacuum pack the module again. Bake the module before mounting components to the module. A.SMT placement equipment: a)Reflow soldering machine; b)Automated optical inspection (AOI) equipment; c)Nozzle with a 6 mm to 8 mm diameter; B. Baking equipment: a)Cabinet oven; b)Anti-static heat-resistant trays; c)Anti-static heat-resistant gloves;
Storage conditions for a delivered module are as follows:: A.The moisture-proof bag is placed in an environment where the temperature is below 30°C and the relative humidity is lower than 70%. B.The shelf life of a dry-packaged product is six months from the date when the product is packaged and sealed. C.The package contains a humidity indicator card (HIC).
Bake a module based on HIC status as follows when you unpack the module package: A.If the 30%, 40%, and 50% circles are blue, bake the module for 2 consecutive hours. B. If the 30% circle is pink, bake the module for 4 consecutive hours. C.If the 30% and 40% circles are pink, bake the module for 6 consecutive hours. D.If the 30%, 40%, and 50% circles are pink, bake the module for 12 consecutive hours.
Baking settings: A.Baking temperature:125±5℃; B.Alarm temperature:130℃; C.SMT placement ready temperature after natural cooling: < 36°C; D.Number of drying times: 1; E.Rebaking condition: The module is not soldered within 12 hours after baking. 5.Do not use SMT to process modules that have unpacked for over three months. Electroless nickel immersion gold (ENIG) is used for the PCBs. If the solder pads are exposed to the air for over three months, they will be oxidized severely and dry joints or solder skips may occur. Tuya is not liable for such problems and consequences.
Before SMT placement, take electrostatic discharge (ESD) protective measures.
To reduce the reflow defect rate, draw 10% of the products for visual inspection and AOI before first SMT placement to determine a proper oven temperature and component placement method. Draw 5 to 10 modules every hour from subsequent batches for visual inspection and AOI.
Recommended Oven Temperature Curve
Perform SMT placement based on the following reflow oven temperature curve. The highest temperature is 245°C. Based on the IPC/JEDEC standard, perform reflow soldering on a module at most twice.
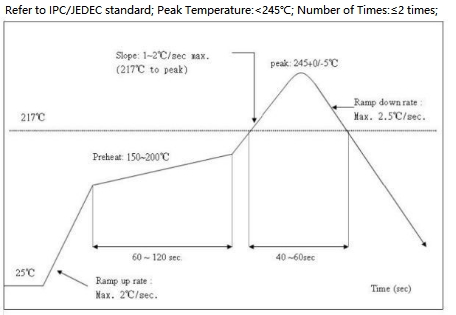
Storage Conditions
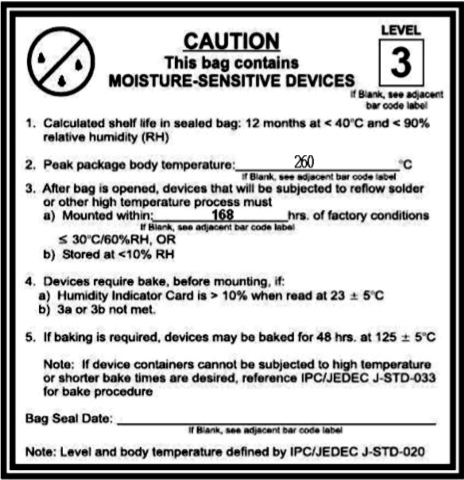
MOQ and Packing Information
Product Model
MOQ(pcs)
Packing Method
Number of Modules in Each Reel Pack
Number of Reel Packs in Each Box
WB3L
4000
Carrier tape and reel packing
1000
4
Appendix: Statement
FCC Caution: Any changes or modifications not expressly approved by the party responsible for compliance could void the user's authority to operate this equipment.
This device complies with Part 15 of the FCC Rules.Operation is subject to the following two conditions: (1) This device may not cause harmful interference, and (2) this device must accept any interference received, including interference that may cause undesired operation.
Note: This equipment has been tested and found to comply with the limits for a Class B digital device, pursuant to part 15 of the FCC Rules.These limits are designed to provide reasonable protection against harmful interference in a residential installation. This equipment generates, uses and can radiate radio frequency energy and, if not installed and used in accordance with the instructions, may cause harmful interference to radio communications. However, there is no guarantee that interference will not occur in a particular installation. If this equipment does cause harmful interference to radio or television reception, which can be determined by turning the equipment off and on, the user is encouraged to try to correct the interference by one or more of the following measures:
—Reorient or relocate the receiving antenna. —Increase the separation between the equipment and receiver. —Connect the equipment into an outlet on a circuit different from that to which the receiver is connected. —Consult the dealer or an experienced radio/TV technician for help.
Radiation Exposure Statement
This equipment complies with FCC radiation exposure limits set forth for an uncontrolled rolled environment. This equipment should be installed and operated with minimum distance 20cm between the radiator and your body.
Important Note
This radio module must not installed to co-locate and operating simultaneously with other radios in host system except in accordance with FCC multi-transmitter product procedures. Additional testing and equipment authorization may be required to operating simultaneously with other radio.
The availability of some specific channels and/or operational frequency bands are country dependent and are firmware programmed at the factory to match the intended destination. The firmware setting is not accessible by the end user.
The host product manufacturer is responsible for compliance to any other FCC rules that apply to the host not covered by the modular transmitter grant of certification. The final host product still requires Part 15 Subpart B compliance testing with the modular transmitter installed. The end user manual shall include all required regulatory information/warning as shown in this manual, including: This product must be installed and operated with a minimum distance of 20 cm between the radiator and user body.
This device have got a FCC ID:2ANDL-WB3L.The final end product must be labeled in a visible area with the following: “Contains Transmitter Module FCC ID: 2ANDL-WB3L”
This device is intended only for OEM integrators under the following conditions:
1)The antenna must be installed such that 20cm is maintained between the antenna and users, and
2) The transmitter module may not be co-located with any other transmitter or antenna.
As long as 2 conditions above are met, further transmitter test will not be required. However, the OEM integrator is still responsible for testing their end-product for any additional compliance requirements required with this module installed.
Declaration of Conformity European notice

Hereby, Hangzhou Tuya Information Technology Co., Ltd declares that this module product is in compliance with essential requirements and other relevant provisions of Directive 2014/53/EU,2011/65/EU.A copy of the Declaration of conformity can be found at https://www.tuya.com
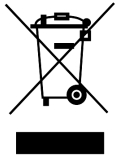
This product must not be disposed of as normal household waste, in accordance with EU directive for waste electrical and electronic equipment (WEEE- 2012/19/EU). Instead,it should be disposed of by returning it to the point of sale, or to a municipal recycling collection point.
The device could be used with a separation distance of 20cm to the human body.
WBLC5 Module Datasheet
Product Overview
WBLC5 is a low-power embedded Wi-Fi and BLE module that Tuya has developed. It consists of a highly integrated RF chip (BK7231T) and several peripheral components, with an embedded Wi-Fi network protocol stack and robust library functions. WB3L is embedded with a low-power 32-bit microcontroller unit (MCU), 2 MB flash memory, 256 KB static random-access memory (SRAM), and extensive peripherals. WBLC5 is an RTOS platform that integrates all function libraries of the Wi-Fi MAC andTCP/IP protocols. You can develop embedded Wi-Fi products as required.
Features
Embedded low-power 32-bit CPU, which can also function as an application processor
Dominant frequency: 120 MHz
Working voltage: 3.0 V to 3.6 V
Peripherals: 3 GPIOs
Wi-Fi connectivity
802.11 b/g/n
Channels 1 to 14 at 2.4 GHz
WPA and WPA2 security modes
Up to +17 dBm output power in 802.11b mode
STA, AP, and STA+AP working modes
EZ and AP net pairing modes for Android and iOS devices
Monopole antenna with a gain of 4.6 dBi
Working temperature: –40°C to +105°C
BLE connectivity
Support for Bluetooth 4.0
Maximum output power of +6 dBm
Monopole antenna with a gain of 4.6 dBi
Applications
Intelligent building
Smart household and home appliances
Smart socket and light
Industrial wireless control
Baby monitor
Network camera
Intelligent bus
Change History
No.
Date
Change Description
Version After Change
1
2019-11-07
This is the first release.
V1.0.0
2
2019-12-10
Modifying typesetting.
V1.0.1
3
2019-12-24
Update BLE related materials
V1.0.2
Module Interfaces
Dimensions and Footprint
WB3L has two rows of pins with a 2±0.1 mm pin spacing. The WB3L dimensions (W x L x H) are 8.5±0.35mm (W)×12.7±0.35mm (L) ×1±0.15mm (H)。
Interface Pin Definition
Pin No.
Symbol
I/O Type
Function
1
ANT
O
External antenna pad pin
2
GND
P
Ground pin
3
PWM4
I/O
Hardware PWM pin, which is connected to the P24 pin on the internal IC
4
PWM5
I/O
Hardware PWM pin, which is connected to the P26 pin on the internal IC
5
PWM0
I/O
Hardware PWM pin, which is connected to the P6 pin on the internal IC
6
VCC
P
Power supply pin (3.3 V)
Note:P indicates a power supply pin, I/O indicates an input/output pin, and AI indicates an analog input pin.
Test Pin Definition
Pin No.
Symbol
I/O Type
Function
TP1
TP1
I/O
RF Test Pin
Note:The test pin is not recommended to use.
Electrical Parameters
Absolute Electrical Parameters
Parameter
Description
Minimum Value
Maximum Value
Unit
Ts
Storage temperature
-20
105
℃
VBAT
Power supply voltage
3.0
3.6
V
Static electricity voltage (human body model)
TAMB-25℃
-
2
KV
Static electricity voltage (machine model)
TAMB-25℃
-
0.5
KV
Working Conditions
Parameter
Description
Minimum Value
Typical Value
Maximum Value
Unit
Ta
Working temperature
-40
-
105
℃
VBAT
Power supply voltage
3.0
3.3
3.6
V
VIL
I/O low-level input
-0.3
-
VCC*0.25
V
VIH
I/O high-level input
VCC*0.75
-
VCC
V
VOL
I/O low-level output
-
-
VCC*0.1
V
VoH
I/O high-level output
VCC*0.8
-
VCC
V
Imax
I/O drive current
-
-
12
mA
Current consumption during constant transmission and receiving
Working Status
Mode
Rate
TX Power/ Receiving
Typical Value
Maximum Value
Unit
TX
11b
11Mbps
+17dBm
292
354
mA
TX
11g
54Mbps
+13.5dBm
256
307
mA
TX
11n
MCS7
+13dBm
257
286
mA
RX
11b
11Mbps
Constant receiving
95
102
mA
RX
11g
54Mbps
Constant receiving
98
100
mA
RX
11n
MCS7
Constant receiving
98
100
mA
Working Current
Working Mode
Working Status (Ta = 25°C)
Average Value
Maximum Value
Unit
EZ
The module is in EZ mode, and the Wi-Fi indicator blinks quickly.
106
386
mA
AP
The module is in AP mode, and the Wi-Fi indicator blinks slowly.
98
405
mA
Connected
The module is connected to the network, and the Wi-Fi indicator is steady on.
58
138
mA
Disconnected
The module is disconnected from the network, and the Wi-Fi indicator is steady off.
40
210
mA
RF Features
Basic RF Features
Parameter
Description
Frequency band
2.412~2.484GHz
Wi-Fi standard
IEEE 802.11b/g/n(channels1-14)
Data transmission rate
11b:1,2,5.5, 11 (Mbps); 11g:6,9,12,18,24,36,48,54(Mbps); 11n: HT20 MCS07; HT40 MCS07
Antenna type
Monopole antenna with a gain of 1.1 dBi
TX Performance
Performance during constant transmission
Parameter
Minimum Value
Typical Value
Maximum Value
Unit
Average RF output power,802.11b CCK Mode 11M
-
16
-
dBm
Average RF output power,802.11g OFDM Mode 54M
-
14
-
dBm
Average RF output power,802.11n OFDM Mode MCS7
-
12
-
dBm
Frequency error
-10
-
10
ppm
RX Performance
RX sensitivity
Parameter
Minimum Value
Typical Value
Maximum Value
Unit
PER<8%,RX sensitivity,802.11b DSSS Mode 11M
-
-85
-
dBm
PER<10%,RX sensitivity,802.11g OFDM Mode 54M
-
-72
-
dBm
PER<10%,RX sensitivity,802.11n OFDM Mode MCS7
-
-68
-
dBm
Antenna Information
Antenna Type
WBLC5 uses a monopole antenna.
Antenna Interference Reduction
To ensure optimal Wi-Fi performance when the Wi-Fi module uses a monopole antenna, it is recommended that the antenna be at least 15mm away from other metal parts.
Packaging Information and Production Instructions
Mechanical Dimensions
The PCB dimensions:8.5±0.35mm (W)×12.7±0.35mm (L) ×1±0.15mm (H)。
Recommended PCB Encapsulation-Pin header
WBLC5 module is inserted and welded。
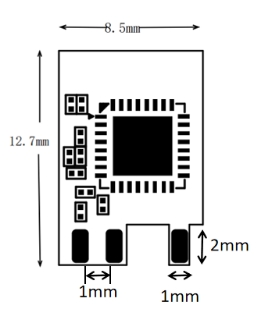
Production Instructions
Use an SMT placement machine to mount components to the stamp hole module that Tuya produces within 24 hours after the module is unpacked and the firmware is burned. If not, vacuum pack the module again. Bake the module before mounting components to the module. A.SMT placement equipment: a)Reflow soldering machine; b)Automated optical inspection (AOI) equipment; c)Nozzle with a 6 mm to 8 mm diameter; B. Baking equipment: a)Cabinet oven; b)Anti-static heat-resistant trays; c)Anti-static heat-resistant gloves;
Storage conditions for a delivered module are as follows:: A.The moisture-proof bag is placed in an environment where the temperature is below 30°C and the relative humidity is lower than 70%. B.The shelf life of a dry-packaged product is six months from the date when the product is packaged and sealed. C.The package contains a humidity indicator card (HIC).
Bake a module based on HIC status as follows when you unpack the module package: A.If the 30%, 40%, and 50% circles are blue, bake the module for 2 consecutive hours. B. If the 30% circle is pink, bake the module for 4 consecutive hours. C.If the 30% and 40% circles are pink, bake the module for 6 consecutive hours. D.If the 30%, 40%, and 50% circles are pink, bake the module for 12 consecutive hours.
Baking settings: A.Baking temperature:125±5℃; B.Alarm temperature:130℃; C.SMT placement ready temperature after natural cooling: < 36°C; D.Number of drying times: 1; E.Rebaking condition: The module is not soldered within 12 hours after baking. 5.Do not use SMT to process modules that have unpacked for over three months. Electroless nickel immersion gold (ENIG) is used for the PCBs. If the solder pads are exposed to the air for over three months, they will be oxidized severely and dry joints or solder skips may occur. Tuya is not liable for such problems and consequences.
Before SMT placement, take electrostatic discharge (ESD) protective measures.
To reduce the reflow defect rate, draw 10% of the products for visual inspection and AOI before first SMT placement to determine a proper oven temperature and component placement method. Draw 5 to 10 modules every hour from subsequent batches for visual inspection and AOI.
Recommended Oven Temperature Curve
Please insert the parts according to the reflow welding curve.Peak temperature is 245℃:
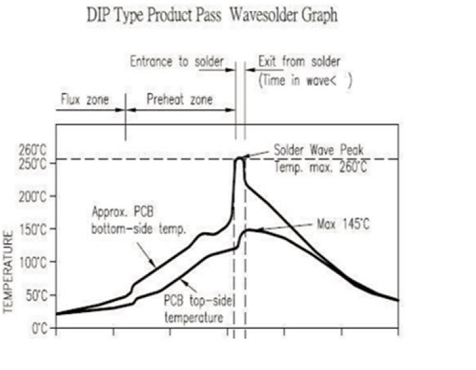
Storage Conditions
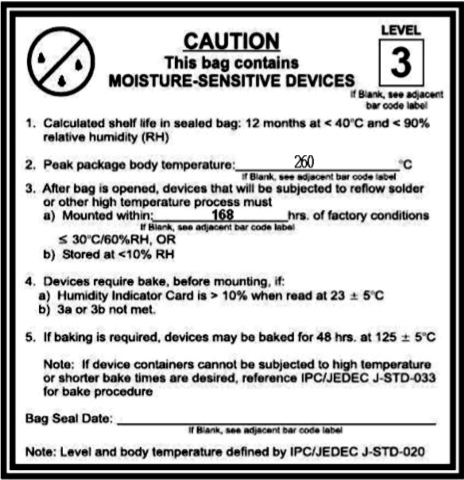
MOQ and Packing Information
Product Model
MOQ(pcs)
Packing Method
Number of Modules in Each Reel Pack
Number of Reel Packs in Each Box
WBLC5
4000
Carrier tape and reel packing
1000
4
Appendix: Statement
FCC Caution: Any changes or modifications not expressly approved by the party responsible for compliance could void the user's authority to operate this equipment.
This device complies with Part 15 of the FCC Rules.Operation is subject to the following two conditions: (1) This device may not cause harmful interference, and (2) this device must accept any interference received, including interference that may cause undesired operation.
Note: This equipment has been tested and found to comply with the limits for a Class B digital device, pursuant to part 15 of the FCC Rules.These limits are designed to provide reasonable protection against harmful interference in a residential installation. This equipment generates, uses and can radiate radio frequency energy and, if not installed and used in accordance with the instructions, may cause harmful interference to radio communications. However, there is no guarantee that interference will not occur in a particular installation. If this equipment does cause harmful interference to radio or television reception, which can be determined by turning the equipment off and on, the user is encouraged to try to correct the interference by one or more of the following measures:
—Reorient or relocate the receiving antenna. —Increase the separation between the equipment and receiver. —Connect the equipment into an outlet on a circuit different from that to which the receiver is connected. —Consult the dealer or an experienced radio/TV technician for help.
Radiation Exposure Statement
This equipment complies with FCC radiation exposure limits set forth for an uncontrolled rolled environment. This equipment should be installed and operated with minimum distance 20cm between the radiator and your body.
Important Note
This radio module must not installed to co-locate and operating simultaneously with other radios in host system except in accordance with FCC multi-transmitter product procedures. Additional testing and equipment authorization may be required to operating simultaneously with other radio.
The availability of some specific channels and/or operational frequency bands are country dependent and are firmware programmed at the factory to match the intended destination. The firmware setting is not accessible by the end user.
The host product manufacturer is responsible for compliance to any other FCC rules that apply to the host not covered by the modular transmitter grant of certification. The final host product still requires Part 15 Subpart B compliance testing with the modular transmitter installed. The end user manual shall include all required regulatory information/warning as shown in this manual, including: This product must be installed and operated with a minimum distance of 20 cm between the radiator and user body.
The RF module is considered as a limited modular transmitter according to FCC rules.Even though the RF module get a FCC ID, the host product manufacturer can not use the FCC ID on the final product directly.In these circumstances, the host product manufacturer integrator will be responsible for re-evaluating the end product (including the transmitter) and obtaining the FCC authorization by a Class II permissive change application or a new application.
Declaration of Conformity European notice

Hereby, Hangzhou Tuya Information Technology Co., Ltd declares that this module product is in compliance with essential requirements and other relevant provisions of Directive 2014/53/EU,2011/65/EU.A copy of the Declaration of conformity can be found at https://www.tuya.com
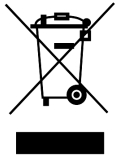
This product must not be disposed of as normal household waste, in accordance with EU directive for waste electrical and electronic equipment (WEEE- 2012/19/EU). Instead,it should be disposed of by returning it to the point of sale, or to a municipal recycling collection point.
The device could be used with a separation distance of 20cm to the human body.
Last updated
Was this helpful?